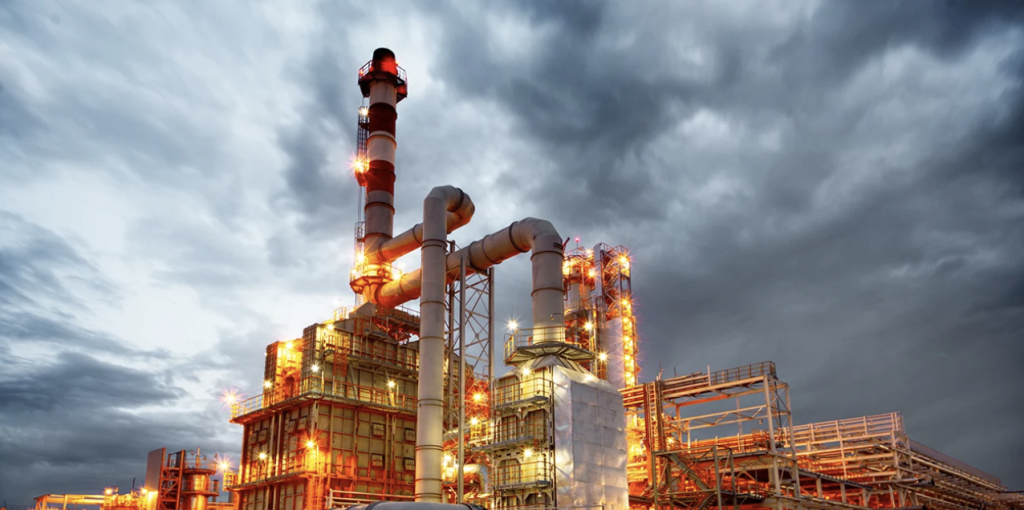
Нефтегазовая промышленность включает в себя дорогостоящие процессы непрерывного производства. Сырье, например сырая нефть, преобразуется в нефтепродукты в очень больших масштабах, что делает контроль таких процессов критически важным. Химические и физические свойства сырья, как правило, сильно различаются, что может оказывать заметное влияние на производительность. Обычно, инженеры используют научные подходы и собственный опыт для определения параметров процесса, которые могут дать желаемые результаты. Однако такая практика часто оказывается плохо воспроизводимой и плохо масштабируемой. В таких случаях статистические контрольные карты могут помочь в отслеживании отклонений в процессах, но даже если получать сигналы об отклонениях от требуемых параметров, это не позволит полностью предотвратить изготовление некачественного продукта.
Что, если бы информацию от поставщика можно было бы использовать для прогнозирования изменений процесса еще до начала работы с сырьем? Это возможно с помощью предиктивных контрольных карт.
Производители перекладывают большую часть ответственности за качество сырья на поставщиков. Но что, если бы информацию от поставщика можно было бы использовать для прогнозирования изменений процесса еще до начала работы с сырьем? В данной статье рассмотрен пример построения и развертывания модели машинного обучения для создания предиктивных контрольных карт. Помимо нефтегазовой отрасли, такой подход также может использоваться при производстве продуктов питания, химических удобрений, а также во многих других отраслях.
В Minitab всего за несколько нажатий мышкой можно создавать точные математические модели, которые могут использоваться для улучшения существующих и разработки новых процессов. Модель процесса создается на основе показателей, полученных от поставщиков, и входных данных процесса. Инженеры определяют необходимое количество входных данных и выбирают тип модели, необходимый для корректного прогнозирования. Готовая модель разворачивается с использованием решения ModelOps от Minitab, после чего в она может работать с потоком данных в автоматическом режиме. Контрольные карты строятся на основе прогнозов модели и контролируют стабильность процесса. Если выявлена неблагоприятная тенденция, модель пересматривается, чтобы найти переменные процесса, которыми можно управлять, чтобы смягчить тенденцию.
В данном примере было задействовано 16 непрерывных переменных, одна из которых представляет собой данные по сертификации сырья от поставщика. Из оставшихся переменных две можно использовать для настройки процесса. Модель множественной регрессии построена на основе 478 записей исторических данных и имеет показатель R-квадрат приблизительно равный 67% (Рис. 1).

На рисунке ниже представлены результаты оптимизации процесса, которые иллюстрируют влияние наиболее важных переменных. Информация о сертификации и начальное давление оказывают сильное влияние на результат, в то время как температура охлаждения и дискретные настройки оказывают не столь сильный эффект (Рис. 2).
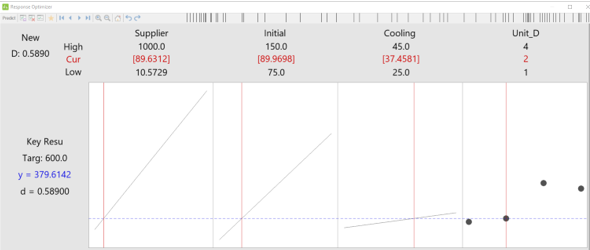
Модель регрессии хорошо справляется с прогнозированием ключевых результатов на исторических данных. Специалисты легко могут развернуть модель в ModelOps из Minitab одним щелчком мыши (Рис. 3).
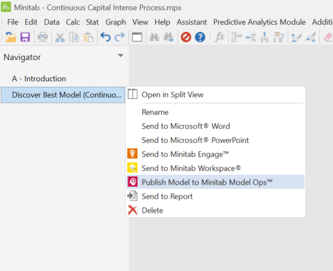
Далее собираются новые данные, чтобы можно было построить прогноз. Данные также включают информацию от поставщика, статические входные значения для настроек и данные, сгенерированные из экспериментального распределения для переменных процесса. Например, температура обработки зависит от настроек управления. Параметры для переменных создаются исходя из измерений и технической спецификаций от производителя оборудования. Такой подход позволяет получить реалистичные сценарии работы по аналогии с методом моделирования Монте-Карло.
Затем Minitab Connect собирает данные и каждый час отправляет их в Model Ops для получения прогнозов. Индивидуальная контрольная карта и карта скользящего размаха используются для отслеживания тенденций. В данном случае важно обеспечить использование исторических параметров для расчета пределов статистического контроля; использование сгенерированных данных для расчета пределов нецелесообразно. Предиктивные контрольные карты демонстрируют, что ожидаемый процесс будет стабильным за исключением 3 последних наблюдений (Рис. 4). Все три конечных наблюдения опустились ниже исторического нижнего контрольного предела, что может создать проблемы с качеством, если такая тенденция сохранится.
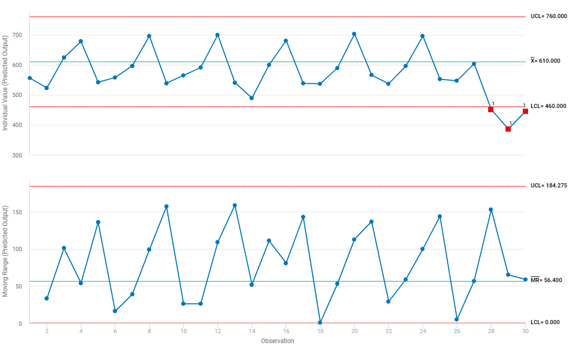
Группа инженеров просматривает модель процесса и определяет, что начальное давление можно увеличить с 90 до 120 единиц. Результаты оптимизации обновленной модели указывают, что изменение давления, вероятно, предотвратит падение выходной характеристики. Предложенное изменение начального значения давления обновляется в модели генерации данных, после чего контрольные карты действительно демонстрируют смягчение негативной тенденции (Рис. 5).
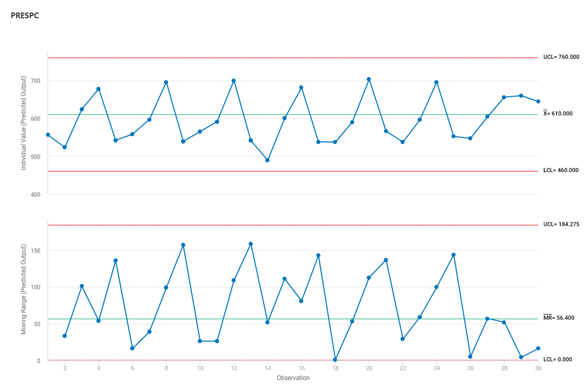
Концепция SPC предполагает своевременную реакцию на меняющиеся тенденции, которые приводят к нестабильности. Нестабильный процесс сопряжен с риском для качества, что может привести к несоответствию или снижению качества материала. Возможность создавать контрольные карты до того, как процесс будет выполнен, невероятно ценна, поскольку теперь можно смягчить неблагоприятные тенденции до того, как будут получены какие-либо фактические результаты. В нефтегазовой отрасли выгоды могут исчисляться миллионами рублей благодаря объему и потенциальному доходу от производимой продукции. Решения Minitab легко превращают процесс создания и мониторинга предиктивного SPC в неотъемлемую часть управления качеством.
Источник: minitab.com